Chemical

At the same time, [MPC] personnel made recommendations for projects, repairs and procedural changes that would reduce the amount of energy used. These suggestions ranged from simple (fix steam leaks) to quite complex (change the operation of a stripping column). The plant team evaluated the recommendation and carried through with implementation. The process of evaluation and training led by [MPC] had a major effect on how the plant viewed energy and its use.
Robert A. Ardoin
Director of Manufacturing
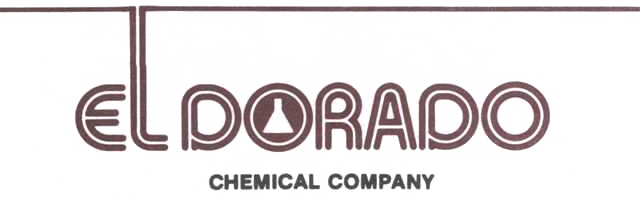
MPC set up models for steam usage, gas usage, and ammonia usage based on historical data. These models contain various drivers for consideration of production rates, weather, and other variables. The energy projects that have been implemented reflect the savings in the models as well as in the invoices received for utilities and raw materials.
Warren Jones
Vice President Administration
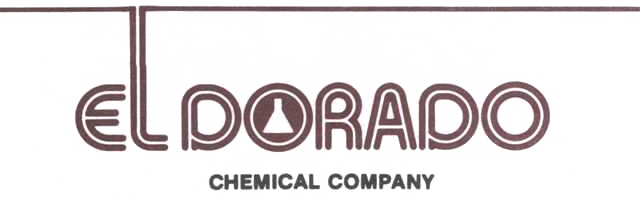
MPC provided quality personnel who actively worked with our plant personnel to identify opportunities and aggressively go after the savings. They provided a system that will allow us to continue to improve savings well after they have gone. In total they were here about 7 months with from 3 to 5 personnel at any one time. They did exactly as they said they would. Their people were professional and easy to work with. The key for a successful outcome requires a commitment and trusts on both sides and can only be successful if both sides benefit. They were strictly business and have saved us about $1,500,000 a year in energy and raw materials usage. We feel confident that we will continue to improve on the saving after they have gone with the tools and knowledge they have given us to work with. I would certainly recommend using them in other locations.
George Hogg
Plant Manager
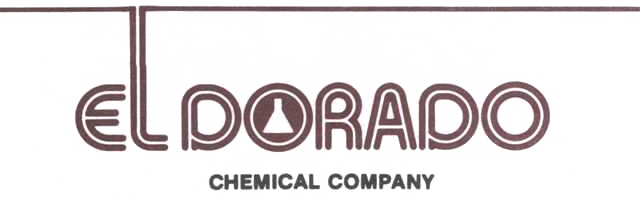
MPC has worked side-by-side with EDCC personnel to develop a detailed understanding of our manufacturing processes and build a solid working relationship to implement positive change. Based on project results to-date, EDCC appears to be reaching its energy reduction goal. We have also seen other corollary program benefits including:
- Improved operations monitoring resulting in better quantification of energy savings opportunities, and a system to implement needed change in a timely manner,
- A proactive and positive attitude within the EDCC organization to identify new energy and raw material savings opportunities, and publicize the successes throughout the organization.
- Reduction of capital expenditures through identification of lower investment alternatives or by reducing energy consumption to the point where a capital project may no longer be justified,
- An upgrade of our energy and raw material metering system that will help EDCC identify future opportunities and retain energy savings already implemented.
Larry D. Fitzwater
Vice President
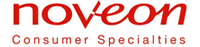
MPC has worked with each area to customize reports to meet the needs of the individual areas, while at the same time developing higher level summaries that provide a basis for consistent comparison across the various businesses. MPC has worked with operating personnel and first line to supervisors to understand how to use the reports and to understand their importance in tracking productivity and driving improvement.
Fred Wohlhuter PH.D.
P.E. Sr. Process Improvement Engineer Akron Plant
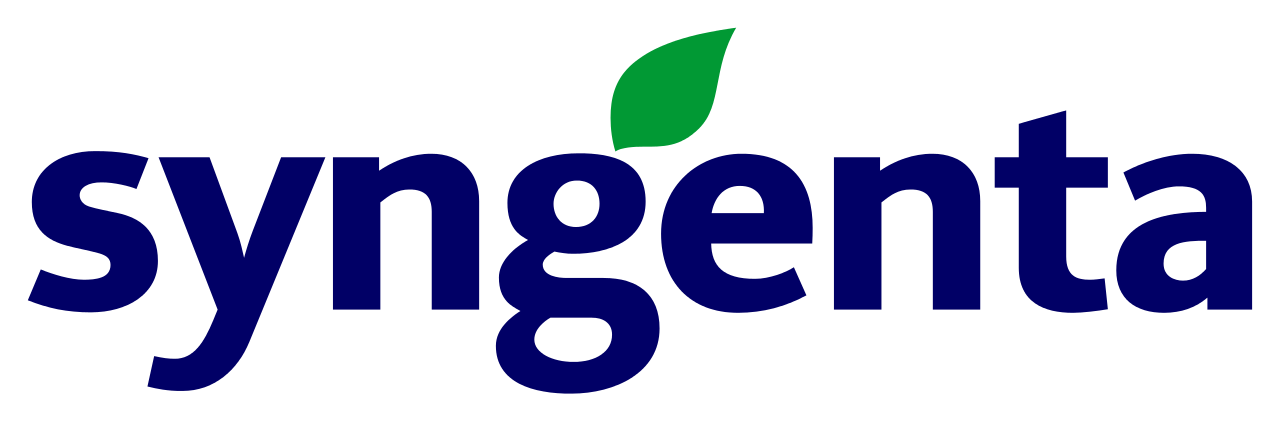
The project has evolved, as expected, around two central themes -major operational improvements that make step changes in consumption and personnel awareness, and knowledge that influences the "continuous improvement" aspects of operations. To achieve the overall 7% decrease in utility consumption that is now the agreed upon goal, both companies had to face significant challenges to their modes of thinking that were in play at project start-up. The great credit to MPC in this process is that they recognized there were many drivers to cost savings at the St. Gabriel Plant and energy savings had to be balanced against a variety of factors including inventory carrying costs and different achievable run rates based on different final products. This adaptive challenge was met and overcome by MPC. Their team changed the normal MPC approach in several ways that fully met Syngenta's needs. This was the key to success - MPC listening and coming to a full understanding of the customer's business. The result is a program in place that will serve St. Gabriel well into the future as the challenges of energy costs continue.
Robert W. Slaven
Site Manager, St. Gabriel Plate Site
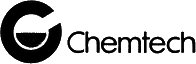
We were impressed with the ability of you and your staff to quickly achieve an understanding of our operation and to develop an identifiable and workable program. The program thus developed was understandable and believable to all employees at SSC, and, therefore, has been achievable. Your ability to work with our people at all levels has been an instrumental part in achieving the above savings.
Jack G. Westberry
Vice President of Operations
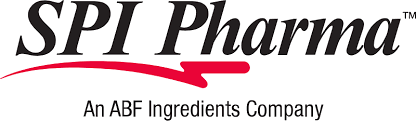
Today, I am seeing sustained energy cost savings equal to your initial estimates. We are much more aware of our energy performance. All of my expectations have been met; I am particularly pleased with the fact that we have been able to sustain the savings on our own.
Paul F. LoPresto
Vice President of Operations

With the receipt of our final project billing, I would like to thank you and the MPC staff for the substantial savings you have helped Sun Chemical attain. Not only have your work and method brought financial benefits, but communications have been opened between departments allowing advances beyond the scope of utility management. I wish you continued success.
Craig S Stucky
Utilities Engineer
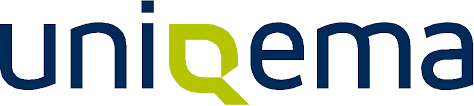
Having tried unsuccessfully in the past internally to create an energy usage model, your ability to capture our complex operation in a model that clearly shows our energy performance is commendable as well. With the model established as our monitoring tool, I am confident the site will have the ability internally to continue to drive improvements and savings well into the future.